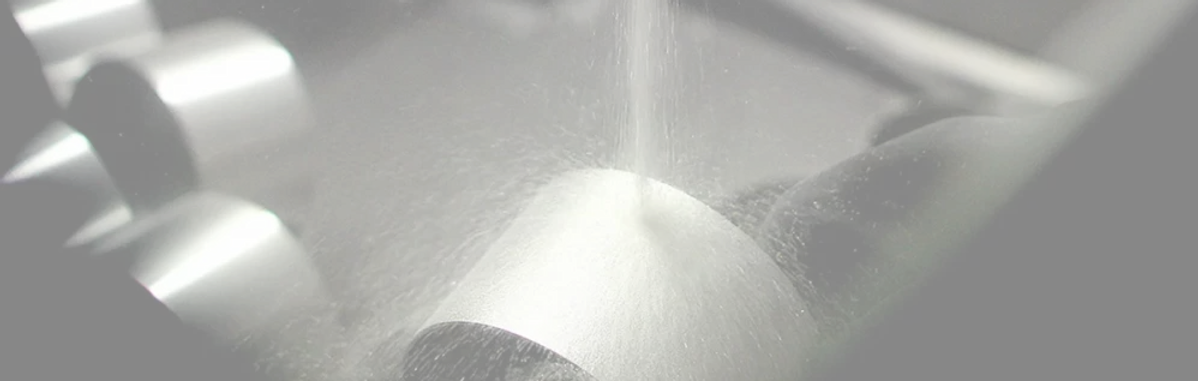
Our Post Processing
​
-
96.67% of all parts delivered first-time-right
-
Services for those who look for transparency, reliability, and consistency.
​​
Post Processes
As-Machined
Ra 3.2, Ra 1.6, Ra 0.8
Anodising
Type I, II, and III
Bead Blasting
+Sand blasting
Polishing
Electro-, or mechanical polishing
Laser- etching
Up to 0,5 mm depth
Brushed
Coarse, Medium, Fine
Powder Coating
Texture and RAL color of your choice
Other Coatings
Chemical blackening , Zinc plating
Production Stages
1. Preparation and Planning
-
Study the design and the materials.
-
Choose appropriate tools and set up the machine.
​
​
2. Manufacturability Discussions
-
Operator to discuss the tool path and tooling with Rototip Engineers
-
Rototip agrees with the customer on potential modifications on the design
3. Programming and Machining
-
Secure the workpiece using fixtures or clamps.
-
Execute machining operations using the G-codes programmed
​
4. Real-time Quality Control
-
With every new operation, monitor dimensions and finish.
-
Operator to address deviations if needed & communicate with Rototip.
5. Post-Machining Inspection
-
Complete full inspection of the part for accuracy and quality.
-
Invite Rototip for FAI (First Article Inspection
-
Deliver the parts to Rototip as per Rototip’s Part Handling guidelines.
6. Packaging and Documentation
-
Rototip to organise additional processes (surface treatments or coatings) if required.
-
Following the final in-house or third-party quality control, Rototip to complete packaging and keep detailed records for traceability.