Unlocking Limitless Possibilities of 3D Printing with SS 316
- Can
- Feb 7
- 3 min read
In manufacturing, precision and material performance often determine the success of a project, especially when parts are subjected to forces in tough environments or used in high-stress conditions. 3D printing in stainless steel using DMLS (Direct Metal Laser Sintering), particularly SS 316 and SS 316L, has become a reliable solution for engineers tackling these challenges.
What makes these materials stand out? Their exceptional corrosion resistance and strength-to-weight ratio have made them a go-to choice for industries requiring durable, high-performing parts with complex geometries that cannot be manufactured using traditional methods.
What’s just as important as the material itself is how it’s applied to solve real-world problems.
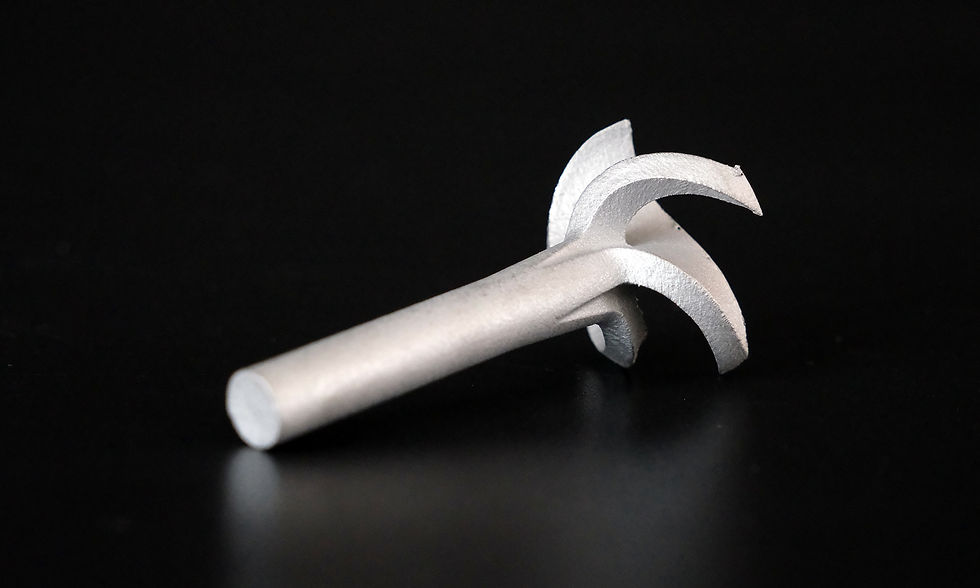
Let’s take a closer look at two projects where 3D-printed SS 316 and SS 316L have helped push the boundaries of mechanical design and innovation.
Project 1: Weeding Robots - Robotic Automation in Farming
One of the more fascinating projects I’ve worked on involves robotic automation for weed control. Imagine robots rolling across a field, using computer vision and applications of mechatronics to identify and remove weeds with over 95% precision. No chemicals, minimal manual labor, just efficient, sustainable farming.
The challenge? These robots operate in harsh outdoor conditions, exposed to dirt, rain, and constant mechanical strain. That’s where SS 316 and SS 316L shine. For this project, we 3D printed custom stainless steel components capable of handling:
Corrosion from moisture and soil exposure.
High mechanical loads from repetitive operations.
Lightweight durability, reducing wear and energy consumption.
Every time I see one of these robots in action, it’s a reminder of how precision engineering can address environmental challenges while increasing efficiency.
Project 2: Industrial Equipment - Strength Behind Every Machine
In another project, we worked for a company supplying machines for industrial applications like sewing, cutting, welding, and engraving.
Their machines needed parts that could:
Perform under intense mechanical stress from continuous use.
Maintain performance and reliability over time.
By leveraging SS 316L 3D printing: DMLS (Direct Metal Laser Sintering), we helped them create components that were both durable and optimized for precise performance they were after.
These custom parts improved:
Seamless assembly, reducing downtime.
Weight reduction, enhancing efficiency.
Resistance to wear, extending the life of their machines.
It’s a great example of how thoughtful design and the right material selection can impact productivity and reliability across industries.
Why Businesses Choose SS 316 and DMLS (Direct Metal Laser Sintering)
As a manufacturing engineer, I see Traditional machining is great for many applications, but it has limitations. This is where DMLS (Direct Metal Laser Sintering) changes the game for businesses.
Instead of cutting away material, DMLS fuses fine metal powder layer by layer using a high-powered laser.
This allows for:
Design Flexibility: Internal cooling channels, lattice structures, and organic shapes that machining can’t achieve.
Material Efficiency: Less waste compared to subtractive manufacturing, reducing overall material costs.
Functional Optimization: Stronger, lighter parts with geometry designed for performance, not just manufacturability.
For designers and engineers, 3D printing is another way of rethinking and improving part design from the ground up.
Shaping the Future of Manufacturing
Every project we take on, whether it’s robots or industrial machines, is a collaboration with innovators who are changing their industries. 3D printing with DMLS in SS 316 and SS 316L is one of the tools we use to help them succeed, especially when it comes to one-off prototyping or low-volume manufacturing.
If you’re exploring new ways to solve engineering challenges, we’re here to share what we’ve learned and help you take your ideas further.