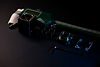
Why work with Rototip?
Quality Control
We provide in-house quality control using a broad selection of our own gauges, calipers, micrometers, and third party laboratories.
Shorter Lead Times
We ensure on-time delivery, offering production as fast as 2 hours for certain applications. We offer speed without any quality compromises.
Regular Updates
No room for last minute surprises, we provide regular updates; keeping you in the loop, always informed, but never overwhelmed.

Initial reviews with DfM
Design for Manufacturability (DfM) review optimizes your designs before production begins. Rototip engineers highlight potential improvements and address challenges. All to ensure your parts are production-ready, saving time and avoiding costly revisions.
Periodic controls during production
Our quality assurance approach is not just an inspection of finished products. Our engineers control and inspect manufacturing processes in workshops with routine visits to the shopfloor and send you production updates, to keep you in the loop without the hassle.

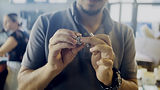
Detailed inspections done in-house
Your parts undergo detailed inspection in our own metrology lab. Using advanced measurement tools and inspection protocols, our engineers verify dimensional accuracy, material properties, and performance to meet your standards.
Reliable Quality for Every Time Right Parts
Our in-house quality inspections ensure precision and consistency. By controlling every step of the process, we guarantee parts meet exact specifications for your peace of mind.
Inspection Capabilities
DFM reports

DFM reports
Manufacturing follow-ups

Manufacturing follow-ups
Material certification
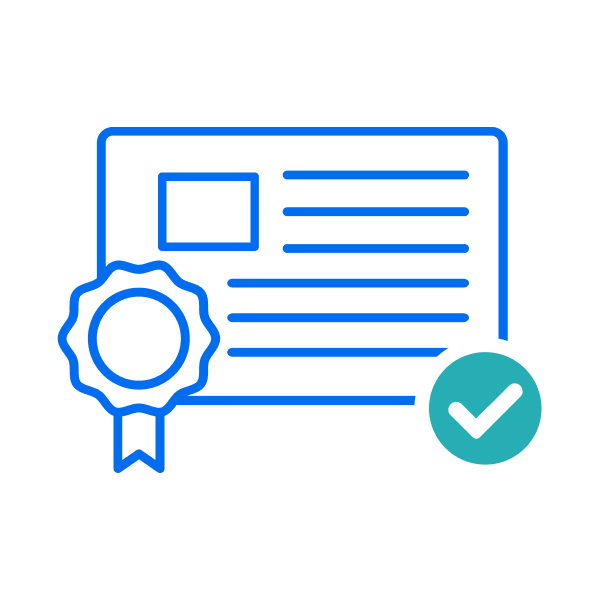
Material certification
Cosmetic inspections

Cosmetic inspections
Dimensional inspections

Dimensional inspections
FAI (First Article Inspection)

FAI (First Article Inspection)
Compliance with spesifications

Compliance with spesifications
Quality control reports

Quality control reports
Packaging controls

Packaging controls
CMM measurements
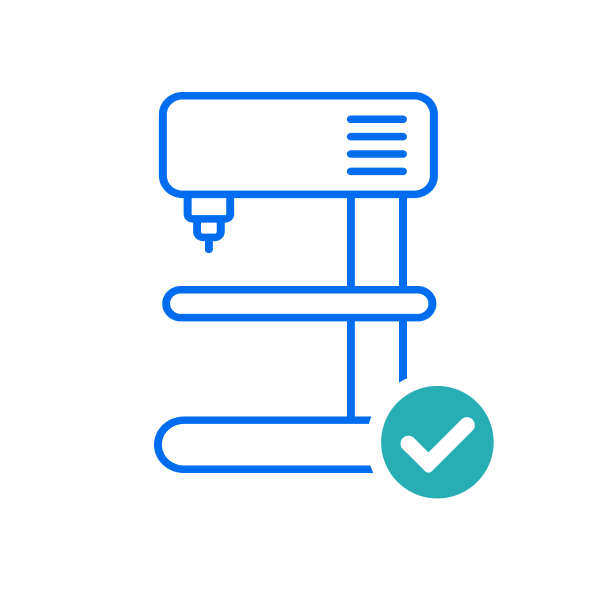
CMM measurements
Non-conformity reports

Non-conformity reports
Post-sale follow-ups

Post-sale
follow-ups
Quality and Transparency at Every Step

Alihan
Project Executive
My work is all about informing customers and supporting them every step of the way, so they can focus on their work while trusting us to handle the details.

Ismail
Manufacturing Team Lead
From the initial DfM to quality handoffs, we aim to deliver the customer needs, exactly right. No compromises. I don’t buy rotten apples at the supermarket.

Tuğçe
Quality Engineer
The quality process isn't just a bunch of checkboxes or symbols on the drawings. I would say it's about building trust with our customers through precision and reliability.
Why choose in-house quality control?
Lorem ipsum dolor sit amet consectetur. Convallis convallis vulputate eget in diam. Viverra semper donec tempus lectus nunc. Pretium ornare netus tincidunt lacus. Quis id ornare mollis morbi.
Visual & Dimensional
Inspection
Lorem ipsum dolor sit amet consectetur. In pellentesque massa urna accumsan purus neque. Suspendisse viverra.
First Article Inspection
Lorem ipsum dolor sit amet consectetur. In pellentesque massa urna accumsan purus neque. Suspendisse viverra.
Material
Inspection
Lorem ipsum dolor sit amet consectetur. In pellentesque massa urna accumsan purus neque. Suspendisse viverra.
Advanced
Inspection
Lorem ipsum dolor sit amet consectetur. In pellentesque massa urna accumsan purus neque. Suspendisse viverra.
-
Which industries you are active in?We serve a wide variety of industries, including: Aerospace, Aviation, Telecommunications: Tight-tolerance light components for aircraft and spacecraft. Industrial Automation & Machinery: Custom components for automation, factory robotics, and heavy machinery. Medical Devices: Custom parts that meet FDA and ISO 13485 standards for medical and healthcare applications. Automotive: Precision parts for electric vehicles and custom interior components.
-
How do I get a quote and place an order?Request a quote Login to our web app at app.rototip.com Enter your account details if you are logging in for the first time Go to the Request Quote page Upload your parts Adjust part specifics Review and submit your inquiry Approve a quote When you wish to proceed with an order, you can either approve the quote over our web app or share with us your purchase order. Production will be initiated in a few hours. Our team will carefully review your request and promptly provide you with a quote. You may also directly email our team at manufacture@rototip.com or urgent@rototip.com about your inquiries.
-
How do you handle intellectual property (IP) and confidentiality?Protecting your intellectual property (IP) is one of our top priorities. All customerfiles, designs, and communications are handled with strict confidentiality and are securely stored. We use encryption protocols to safeguard your data both in transit and at rest with only authorized personnel having access to sensitive information. Your designs are never distributed to more than a couple of engineers and operators who need to see the drawings because they will most likely be working on the production.
-
How do you ensure parts meet the quality requirements?We adhere to a quality management system that ensures every part meets the required specifications. Our process includes: Material supplier selection: We work with a select group of suppliers providing us the required materials in the right form and size. Depending on our history with each supplier, the materials we procure are tested for chemical composition, strength, hardness, and more. Selection of the machine and operator: Among all the workshops we work with, we work with and train an algorithm that awards the manufacturing of parts depending on the customer, material, geometry, tolerances, lead time, and quantity. Upon selection, our own engineers work with the operator throughout the production process from the initial CAM engineering to the deburring of the parts. Defining of quality control process & equipment: Together with our project managers and manufacturing engineers, our own quality engineers work out a detailed quality control plan specifying the following details, just to name a few: List of our quality equipment will be used during the process The percentage of parts that will be inspected visually, with caliper, with micrometers and other handheld devices, and/or on a CMM if any, list of measurements that cannot be measured Packaging: We operate with a detailed packaging guideline, clarifying how parts should be packaged, tagged, documented, and shipped. First Article Inspections (FAI): To ensure that the first part produced matches your exact design, we will ship you the first parts manufactured. Only after the client’s approval will we proceed with the production of the entire order. Final Inspection: All parts are inspected for dimensional accuracy, surface finish, and mechanical integrity before shipment. Certification Compliance: We possess ISO 9001 to ensure the highest levels of quality. Should you have any further questions, please drop us an email at quality@rototip.com.
-
What are your standard lead times?Lead times depend on the manufacturing process, material selection, and complexity of the part, among many others. For urgent inquiries and rather simple geometries, we offer manufacturing services as quickly as 2 hours. See below a table summarising our common offerings: Please contact us at manufacture@rototip.com or reach out to your account manager to discuss special requirements or other manufacturing technologies.